Roofing Machines: Boosting Speed, Accuracy & Safety in Roof Installation
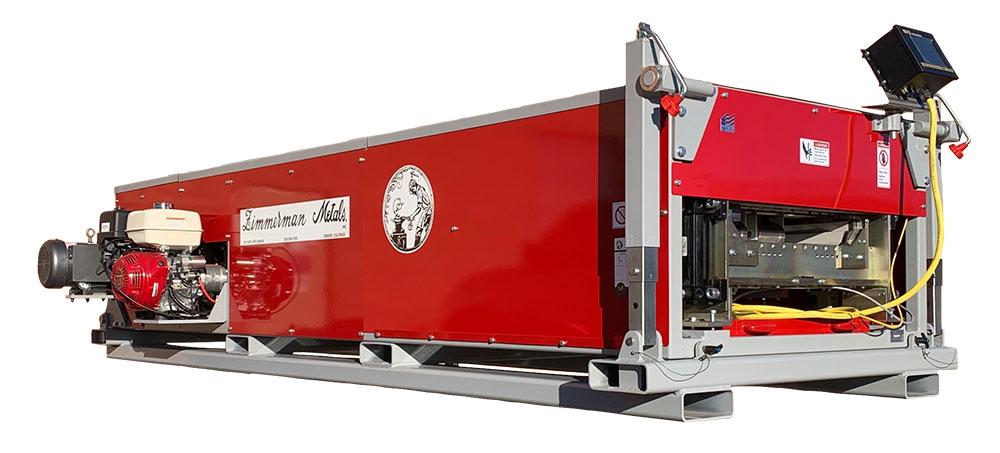
The roofing industry has evolved significantly over the past few decades, driven by advancements in technology, materials, and installation methods. One of the most impactful innovations revolutionizing the way professionals approach roofing is the development and widespread use of roofing machines. These machines have transformed roof installation by improving speed, accuracy, safety, and profitability for contractors and manufacturers alike.
What Are Roofing Machines?
Roofing machines are specialized mechanical tools and equipment designed to automate or assist with different aspects of the roofing process. These machines are primarily used for forming roofing materials (like metal panels), fastening roofing components, and seaming joints.
By reducing the reliance on manual labor, roofing machines not only boost productivity but also ensure greater consistency and precision, two factors that are vital in modern construction.
Types of Roofing Machines
There are different types of roofing machines tailored to specific roofing systems and tasks. Here are the most common ones:
- Roll Forming Machines
Roll forming machines are used to fabricate metal roofing panels on-site or in a workshop. They shape coils of metal into specific roofing profiles like standing seam panels or corrugated sheets.
- On-site panel creation minimizes waste and transportation costs.
- Custom lengths eliminate the need for additional trimming or seams.
- Ideal for residential, commercial, and industrial roofing systems.
- Seaming Machines
Seaming machines are essential for standing seam metal roofing systems. They join adjacent panels by crimping the seams together for a water-tight and wind-resistant bond.
- Ensure consistent, strong seals.
- Save time compared to manual seaming tools.
- Available in mechanical and battery-powered versions.
- Automatic Fastening Machines
These machines automatically drive screws or fasteners into panels, reducing worker fatigue and ensuring uniform placement.
- Improve installation speed.
- Reduce installation errors.
- Enhance structural integrity.
- Membrane Roofing Welders
Used for flat or low-slope roofs, these machines heat-weld TPO, PVC, or EPDM membrane seams.
- Provide consistent weld strength.
- Eliminate manual errors.
- Improve weather resistance.
- Shingle Cutting Bending Machines
These assist in shaping and customizing asphalt shingles or metal roofing accessories for precise installations around edges, ridges, and valleys.
Key Benefits of Roofing Machines
✅ 1. Improved Speed and Efficiency
Roofing machines drastically reduce the time required to complete projects. With on-site roll forming or automated fastening, contractors can complete roofs in a fraction of the time.
- Complete more jobs in less time.
- Reduce labor costs.
- Meet tight deadlines with ease.
✅ 2. Precision and Consistency
Manual labor is prone to inconsistencies, especially on large projects. Roofing machines deliver precise cuts, seams, and fastening patterns — improving quality and reducing the need for corrections.
- Professional-looking results.
- Less material waste.
- Fewer callbacks and repairs.
✅ 3. Enhanced Safety
Machines reduce the amount of time workers spend on ladders or rooftops, decreasing the risk of accidents. Additionally, automated tools reduce physical strain.
- Improve on-site safety.
- Lower insurance and liability costs.
- Reduce worker fatigue.
✅ 4. Customization and Flexibility
On-site roll forming machines allow custom panel lengths and profiles, accommodating unique roof designs and architectural requirements.
- Adapt to changing project demands.
- Offer bespoke roofing solutions.
- Reduce reliance on third-party suppliers.
✅ 5. Long-Term Cost Savings
Although roofing machines require an initial investment, they quickly pay for themselves through labor savings, material efficiency, and increased job capacity.
- Higher ROI over time.
- Fewer delays and rework.
- Increased project profitability.
Considerations When Investing in Roofing Machines
Before adding roofing machines to your equipment lineup, consider the following:
- Type of roofing services you offer (metal panels, membrane systems, shingles).
- Volume of projects—larger or frequent jobs justify the investment.
- Portability—some machines are trailer-mounted for on-site use.
- Training requirements for your team to operate the machines safely.
- Maintenance and warranty are provided by the manufacturer.
Choosing the right machine from a trusted supplier is crucial to maximizing performance and value.
Roofing Machines and Sustainability
Roofing machines support green building efforts by:
- Reducing material waste.
- Allowing for recyclable metal roofing production.
- Enabling tighter-fitting, energy-efficient installations.
As building codes evolve and sustainability becomes more important, machines that produce energy-efficient and long-lasting roofing solutions will only grow in demand.
The Future of Roofing Machines
The roofing industry is seeing exciting innovations in automation and machine integration:
- Battery-powered seamers and welders for remote or off-grid use.
- Digital panel design software integrated with roll formers.
- AI-enhanced measuring tools for greater accuracy.
- IoT-enabled machines for tracking usage and maintenance.
These technologies not only streamline operations but also improve safety and reduce errors — making roofing faster, smarter, and safer.
Final Thoughts
Roofing machines are reshaping the future of the roofing industry. By increasing speed, precision, and safety, these tools allow contractors to deliver higher-quality work in less time and with fewer resources. Whether you're a small roofing business or a large-scale contractor, investing in the right machines can give you a major competitive edge.
- Art
- Causes
- Crafts
- Dance
- Drinks
- Film
- Fitness
- Food
- Spellen
- Gardening
- Health
- Home
- Literature
- Music
- Networking
- Dating & Match Making
- Party
- Religion
- Shopping
- Sports
- Theater
- Wellness