Maximize ROI with Timely Power Transformer Testing
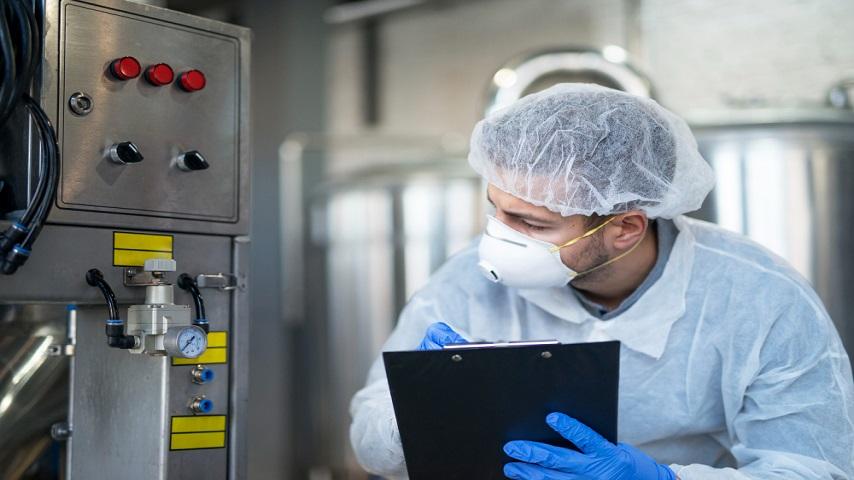
In the world of electrical infrastructure, power transformers are among the most critical—and most expensive—assets. They sit at the heart of substations and industrial plants, quietly stepping voltage up or down to keep operations running. But when a transformer fails, the result is not just downtime—it’s costly repairs, production losses, and sometimes catastrophic damage.
Fortunately, these risks can be minimized, and even eliminated, with timely power transformer testing. When done proactively and consistently, testing doesn’t just prevent failures—it protects your investment and maximizes return on it.
Understanding the Value of a Power Transformer
Power transformers are long-term assets that often have a design life of 25–40 years. But like all equipment, their performance degrades over time due to:
- Load stress
- Environmental conditions
- Insulation aging
- Internal faults or winding movement
Neglecting to test or monitor these issues can reduce the transformer's life, increase operating costs, and lead to unscheduled failures.
That’s where transformer testing becomes an investment—one that pays off through extended life, improved reliability, and smarter maintenance strategies.
The Real ROI of Transformer Testing
When considering ROI, it's not just about how much you spend—but how much you save by avoiding preventable costs. These include:
- Unplanned Outages: Equipment failure can halt entire operations, leading to loss of productivity and revenue.
- Emergency Repairs: Last-minute fixes are typically more expensive than scheduled maintenance.
- Asset Replacement: A transformer that could have lasted 10 more years may have to be replaced early due to neglected testing.
- Insurance Premiums: Regular testing and documentation can reduce liability and insurance costs.
- Safety Risks: Testing helps avoid explosions, oil leaks, and fire hazards associated with aging transformers.
By identifying minor issues before they escalate, transformer testing helps you spend less and earn more from the same equipment.
What Does Transformer Testing Involve?
Effective testing covers both routine diagnostics and predictive maintenance. Key tests include:
1. Insulation Resistance (IR) Testing
Measures the condition of the transformer’s insulation system. A drop in resistance can indicate moisture ingress or insulation degradation.
2. Tan Delta (Power Factor) Testing
Evaluates the health of insulation materials. High tan delta values signal insulation aging or contamination.
3. Turns Ratio Testing
Checks the winding ratio between the primary and secondary coils. Any deviation could indicate a shorted or open winding.
4. Sweep Frequency Response Analysis (SFRA)
Detects mechanical displacements or winding deformations—critical after a fault or transportation.
5. Oil Analysis (DGA – Dissolved Gas Analysis)
One of the most valuable predictive tools, DGA identifies gases generated by overheating, arcing, or insulation breakdown.
6. Winding Resistance & Impedance Testing
Reveals internal connection issues or shorted turns, especially useful during commissioning or after overload events.
Each test offers a unique window into transformer health, and when combined, they create a comprehensive diagnostic picture.
When Should Testing Be Done?
Transformer testing isn’t a one-time activity. To truly protect your investment, follow a structured testing schedule:
- During Commissioning: Confirm all parameters are within safe operating limits.
- Annually: Perform IR, tan delta, and oil testing to monitor aging trends.
- Post-Fault or Event: After overloads or trips, perform SFRA and resistance tests to rule out hidden damage.
- Before Warranty Expiry: Conduct detailed tests to validate equipment condition.
- Before and After Relocation: Mechanical stress during transport can damage windings.
Predictive Maintenance: The Modern Approach
Traditional maintenance is reactive—fixing problems only after they occur. In contrast, predictive maintenance, driven by timely transformer testing, focuses on early detection and cost prevention.
By integrating test data with historical trends and digital monitoring, you can:
- Forecast transformer life expectancy
- Plan replacements in advance
- Schedule shutdowns without affecting production
- Avoid unnecessary servicing
This leads to lower total cost of ownership (TCO) and a better ROI over the transformer’s lifespan.
Common Mistakes That Undermine ROI
Avoid these costly oversights:
- Skipping routine testing due to budget cuts
- Relying on visual checks alone
- Using outdated or non-calibrated test equipment
- Ignoring minor test deviations, which can worsen over time
- Lack of documentation or trend analysis to track performance changes
Timely transformer testing is only valuable when it is systematic, accurate, and acted upon.
Conclusion: Testing Today, Profits Tomorrow
Your power transformer is not just an electrical component—it’s a long-term financial investment. Like any high-value asset, it requires attention, monitoring, and preventive care.
Timely transformer testing is not an expense—it’s a strategy.
It protects productivity, reduces risk, extends equipment life, and ensures that every dollar you spend on your power infrastructure works harder for your business.
From Safety to Savings: The Full Value of Power System Analysis
Avoiding the Unexpected: Downtime Prevention with Transformer Testing
- Art
- Causes
- Crafts
- Dance
- Drinks
- Film
- Fitness
- Food
- Παιχνίδια
- Gardening
- Health
- Κεντρική Σελίδα
- Literature
- Music
- Networking
- Dating & Match Making
- Party
- Religion
- Shopping
- Sports
- Theater
- Wellness