The Secret to Professional DST Files: Digitizing Techniques the Pros Use
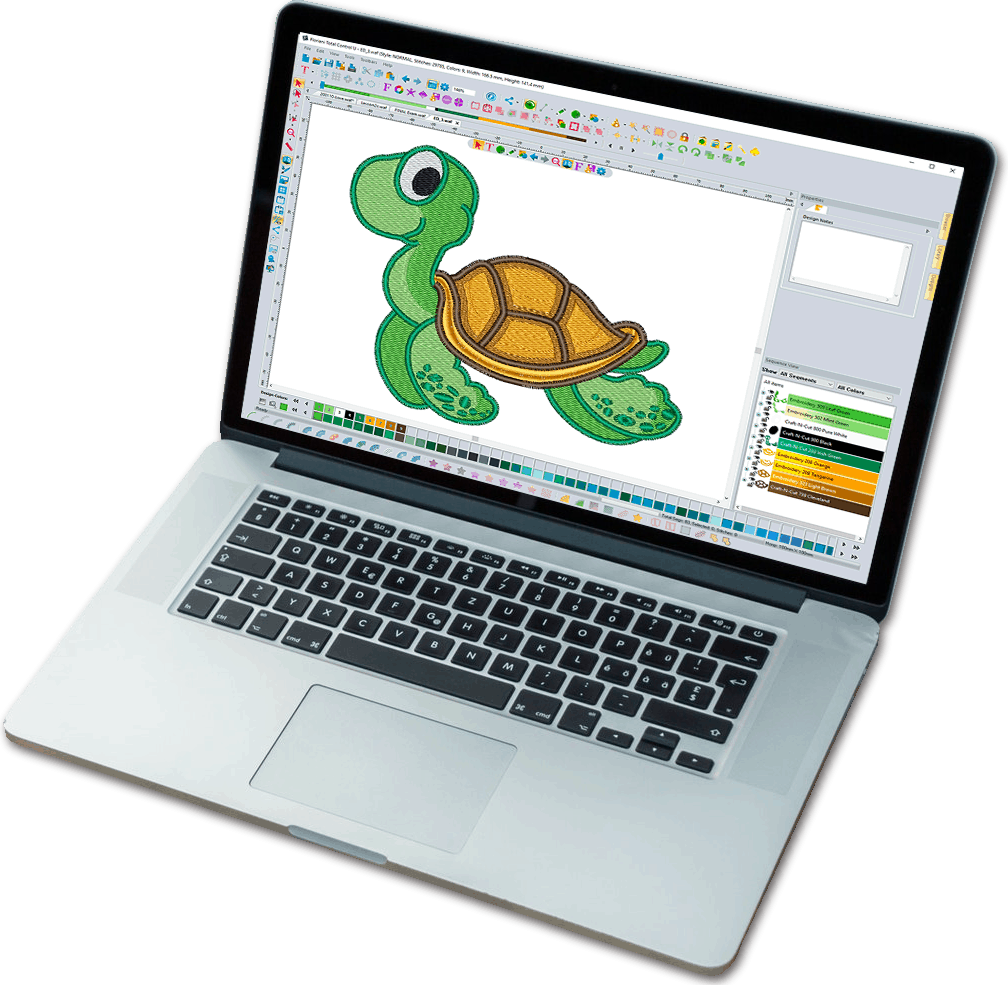
Introduction
What separates an amateurish embroidery file from one that stitches out perfectly every time? The answer lies in how the design gets digitized into that DST file through proper DST digitizing techniques. While anyone can convert an image to DST format, professionals use specific DST digitizing methods to ensure crisp details, smooth curves, and trouble-free stitching.
In this comprehensive guide to DST digitizing, we'll reveal:
-
The 5 most critical digitizing decisions that affect DST quality
-
Little-known software settings the pros always adjust in DST digitizing
-
How to avoid the 3 most common DST file mistakes
-
Advanced DST digitizing techniques for complex designs
-
The truth about auto-digitizing vs. manual methods for DST files
Whether you're creating DST files for your own projects or for clients, mastering these professional DST digitizing techniques will take your embroidery to the next level.
Why DST Files Need Special Attention
DST (Tajima) remains the industry standard format, but it has unique characteristics that affect quality:
Key DST File Challenges:
-
Limited editability - Once saved, difficult to modify
-
Stitch count restrictions - Some machines have limits
-
Precision requirements - Small errors magnify when stitched
How Professionals Compensate:
-
Work in editable formats first (like EMB or PES)
-
Optimize stitch paths to minimize jumps
-
Add manual compensation for fabric pull
The 5 Critical Digitizing Decisions
1. Stitch Type Selection
Fill Stitches:
-
Use for large areas
-
Adjust density based on fabric (0.35-0.45mm typical)
-
Change angle for visual interest
Satin Stitches:
-
Ideal for borders and text
-
Keep width under 8mm for stability
-
Use consistent spacing
Running Stitches:
-
Best for fine details
-
Minimum length 1.2mm
-
Use triple stitch for strength
2. Underlay Strategy
Types of Underlay:
-
Center Run - Basic stability
-
Edge Run - Prevents outline distortion
-
Zigzag - For stretchy fabrics
Pro Tip: Always match underlay type to your top stitches
3. Pull Compensation
What It Fixes:
-
Fabric distortion during stitching
-
Misaligned design elements
How To Adjust:
-
Add 5-15% extra width
-
Varies by fabric type
-
Test on actual material
4. Stitch Sequencing
Golden Rules:
-
Stitch background elements first
-
Work from center outward
-
Minimize jumps between sections
5. Tie-Offs and Trims
Professional Touches:
-
Add extra tie-off stitches
-
Program automatic trims
-
Bury thread tails when possible
Software Settings Pros Always Change
Wilcom Hatch Secrets:
-
Stitch Processor settings for smoother curves
-
Short Stitch Removal to prevent thread breaks
-
Auto-Flow for better fill patterns
Pulse Ambassador Tweaks:
-
Stitch Sculpting for dimensional effects
-
Dynamic Pull Compensation
-
Micro Stitch adjustments
Brother PE-Design Must-Dos:
-
Stitch Balance adjustment
-
Pattern Stitch optimization
-
Jump Stitch reduction
The 3 Most Costly DST Mistakes
1. Ignoring Fabric Characteristics
Solution:
-
Create separate versions for different materials
-
Test on actual fabric before production
2. Overlooking Hoop Size
Solution:
-
Design within safe stitching area
-
Account for 5mm margin all around
3. Relying Only on Auto-Digitizing
Solution:
-
Use auto as starting point only
-
Manually clean up problem areas
-
Adjust stitch-by-stitch where needed
Advanced Techniques for Complex Designs
Photorealistic Embroidery:
-
Convert to 3-5 color layers
-
Use directional fills to mimic shading
-
Add texture with specialty stitches
Small Text That Stays Readable:
-
Minimum 6mm height
-
Bold, simple fonts work best
-
Add outline stitches for definition
Seamless Repeating Patterns:
-
Perfect overlap at edges
-
Match stitch angles across repeats
-
Test multiple hoopings
Auto-Digitizing vs. Manual: The Truth
When Auto Works:
-
Simple designs with clear edges
-
Time-sensitive projects
-
First drafts for manual refinement
When Manual is Mandatory:
-
Complex artwork
-
Critical branding elements
-
Specialty fabrics
Hybrid Approach:
Most professionals:
-
Start with auto-digitizing
-
Clean up major issues
-
Fine-tune manually
Testing and Quality Control
The Pro's Testing Protocol:
-
Stitch Simulation - Check digitally first
-
Scrap Fabric Test - Use actual material
-
Color Verification - Under proper lighting
-
Wash Test - For production items
Red Flags to Watch For:
-
Puckering fabric
-
Thread breaks
-
Color bleeding
-
Misaligned elements
Maintaining DST File Quality
Version Control:
-
Use clear naming conventions
-
Store iterations separately
-
Document changes
Long-Term Storage:
-
Keep original editable files
-
Save in multiple locations
-
Archive with project details
When to Outsource Digitizing
Consider professional digitizing when:
-
Design has complex shading
-
Working with difficult fabrics
-
Need rush turnaround
-
Producing large quantities
Average cost: $15-$50 per design
Conclusion
Creating professional-quality DST files isn't about fancy software—it's about mastering fundamental techniques:
-
Make intentional stitch choices - Don't just accept defaults
-
Compensate for fabric behavior - Test on actual material
-
Manual refinement matters - Auto-digitizing is just a start
-
Develop a testing routine - Never skip quality checks
The difference between an okay DST file and a great one comes down to these professional practices. Start implementing them today, and watch your embroidery quality transform.
Remember: Even experts started somewhere. Pick one technique to focus on each project, and soon you'll be creating DST files that rival the pros.
- Art
- Causes
- Crafts
- Dance
- Drinks
- Film
- Fitness
- Food
- Jogos
- Gardening
- Health
- Início
- Literature
- Music
- Networking
- DATING
- Party
- Religion
- Shopping
- Sports
- Theater
- Wellness